HOW TO IMPROVE TOOL LIFE WHEN TURNING?
The three main machining parameters for turning are speed, feed rate and depth of cut. Each of them has an impact on the life of the tool.
For the best tool life:
- Reduce cutting speed, vc (to reduce heat).
- Optimize feed rate, fn (for shortest cutting time).
- Optimize the depth of cut, ap (to reduce the number of cuts).
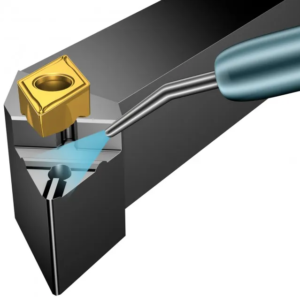
Cutting speed, vc
Too low
- Built-in edge
- Wear of goods
- Uneconomical
- Weak surface
Too high
- Rapid edge wear
- Poor finish
- Rapid wear of the crater
- Plastic deformation
The cutting speed, vc, strongly affects the tool life. Adjust vc for best saving vc.
(Y tool life)
Feed rate, fn
Too low
- Stringers
- Rapid edge wear
- Built-in edge
- Uneconomical
Too high
- Less chip control
- Poor surface treatment
- Crater wear / plastic deformation
- High power consumption
- Chip welding
The fn shift has less of an effect on tool life than vc.
(Y tool life)
Depth of cut, ap
Too small
- Less chip control
- Vibrations
- Excessive heat
- Uneconomical
Too deep
- High power consumption
- Increased cutting forces
- Breaking teeth
The depth of cut, ap, has little effect on tool life.
(Y tool life)
Are you interested in turning services?
See our offer:
For all questions we are at your disposal:
Tool maintenance
Establishing a tool maintenance routine in the workshop will improve tool life during turning, prevent problems, and save money.
Check the insert seat
It is important to ensure that the cartridge is not damaged during processing or handling.
Find:
- Oversized pockets due to wear. The cartridge is not installed correctly on the sides of the pocket. Use 0.02 mm (0.0008 inch) to check the gap.
- There are no gaps in the corners between the base and the bottom of the pocket.
- Damaged washers. Washers must not have cut corners in the cutting area.
- Washer wear due to chip breakage.

Check the insert seat
Make sure that no dust or shavings are formed on the cartridge during processing. If necessary, insert a seat with compressed air. If drill rods with cutting heads are used, it is also important to check and clean the coupling between the head and the rod when replacing the cutting head.
Torque wrench
A torque wrench must be used to properly tighten the insert for optimal operation of the tool holders with screw clamps. Use the recommended torque for each tool holder.
- Excessive torque will adversely affect the operation of the tool and cause the cartridge and screw to break.
- Too low torque causes insert movement, vibration and worsens the cutting result.

Clamping screws
Always use a torque wrench to tighten the screws correctly. Use sufficient lubrication of the screw to prevent the screw from getting stuck. The lubricant must be applied to both the screw threads and the surface of the screw head. Replace worn or damaged screws.
Source: Sandvik Coromant