DRILLING OPERATIONS
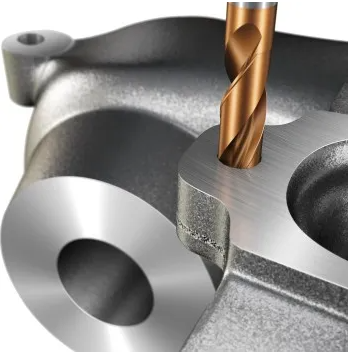
Achieving the required hole quality at the lowest cost per drilled hole depends on the correct choice of tool. These different types of holes require different tool considerations:
- • Small to medium diameter holes
- • Large diameter holes
- • Deep holes
- • Micro holes
Drilling small to medium diameter holes
When drilling small to medium-sized holes, you can choose from three different drilling solutions: hard carbide drill bits, interchangeable tip drill bits and insert inserts. Tolerance, length and hole diameter are three important parameters to consider when choosing the type of drill bit. Each solution has its advantages in different applications.

Drilling large holes
There are three options for drilling large holes with limited machine power:
- • Use the trepanning tool
- • Enlarge the hole with a drilling tool
- • Use spiral interpolation with milling tools
Stability of the component and the machine is important when drilling large holes. The power and torque of the machine can also be limiting factors. In terms of productivity, drilling tools are a top choice - 5 times faster than milling a hole with spiral interpolation. However, the trepanning tool can only be used in applications through holes. Milling cutters have the lowest power and torque requirements to date.
Drilling deep holes

Drilling a pilot hole
Pilot drills are designed to work with deep hole drills, ensuring maximum precision at the drilling site and minimum hole leakage.
Speed and displacement
The speeds and feeds recommended for use with deep hole drills are calculated to ensure good tool life and maximum productivity. Given speeds and passes are a good starting point; for optimal results, each application may require speed and feed adjustments.
Drilling micro holes

Speed and displacement
The speeds and feeds recommended for use with micro drills are calculated to ensure good tool life combined with maximum productivity. Given speeds and passes are a good starting point; for optimal results, each application may require speed and feed adjustments.
Refrigerant
Coolant pressure is a key factor in micro drilling. Improper coolant pressure or volume can lead to premature tool failure. We recommend the use of high coolant pressure. The typical recommended pressure should be between 40-70 bar.
Are you interested in turning services?
See our offer:
For all questions we are at your disposal: